This page contains automatically translated content.
Prüflabor für Eigenspannungs-Analysen an der Uni Kassel
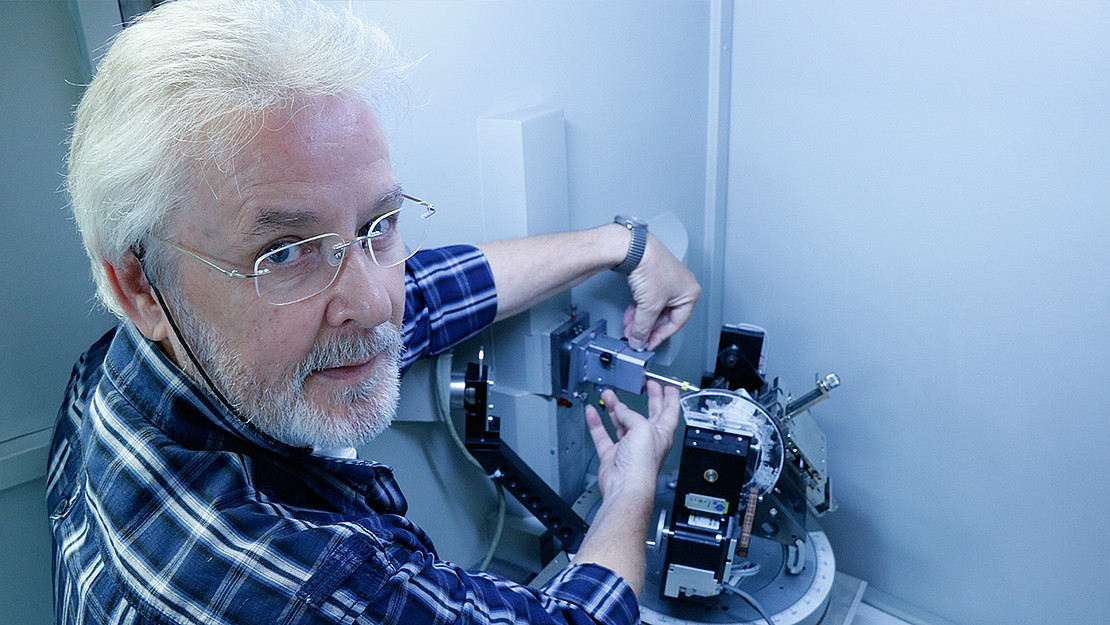
Schon seit etlichen Jahren führt das Institut für Werkstofftechnik/Metallische Werkstoffe im Rahmen des Zentrums für Randschichtanalyse und -technik (ZerTech) Analysen für Projektpartner aus der weltweiten Industrie durch. Das umfasst die Analyse aller metallischen und vieler anderer kristalliner Werkstoffe mit verschiedenen Methoden. Deutschlandweit ist das Prüflabor damit das drittgrößte seiner Art. Seit Juli 2017 ist das ZerTech nun von der Deutschen Akkreditierungsstelle GmbH als Prüflabor für Eigenspannungs-Analysen akkreditiert. Das ist für viele Industrieunternehmen eine Voraussetzung für gemeinsame Projekte in Forschung und Entwicklung.
Eigenspannungen sind innere Spannungen in Werkstoffen. Sie treten als Folge der Herstellung auf, ohne dass äußere Beanspruchungen wirken, etwa wenn sich die Oberfläche eines Werkstücks schneller abkühlt als der Kern. Für das Auge sind sie unsichtbar, sie können aber die Beständigkeit eines Bauteils beeinflussen. Eigenspannungs-Analysen sind daher ein wichtiger Schritt in der Entwicklung sicherer Bauteile und tragen dazu bei, Unfälle zu verhindern.
„Beim Thema Eigenspannungen gilt wie in vielen Bereichen des Lebens: kleine Ursache, große Wirkung“, beschreibt es Dr. Wolfgang Zinn, Leiter des ZerTech. Bereits kleine Fehler oder Anpassungen im Herstellungsprozess von Bauteilen können zu maßgeblichen Änderungen im Eigenspannungszustand führen und so letztlich verheerende Auswirkungen auf die Sicherheit und Zuverlässigkeit von Maschinen haben, etwa wenn ein Zahnrad plötzlich versagt.
In den Laboren des Instituts für Werkstofftechnik wird zu Ursachen und Wirkungen von Eigenspannungen geforscht. Um sie – als Voraussetzung – sicher messen zu können, wurden in den vergangenen Jahren zusammen mit Forschungspartnern neue Methoden und Auswerteroutinen zur Eigenspannungs-Analyse entwickelt, die beispielsweise Röntgenstrahlung nutzen. Auch aus Prüfaufträgen aus der Industrie werden immer wieder neue wissenschaftliche Fragestellungen abgeleitet.